Small Carving Axe, 0.54 kg (1.19 lbs)
Straight Gouge (Rounded Chisel), 10 - 45 mm (0.4 - 1.8 inches)
Hand-Forged Sloyd Knife, 9 cm (3.54 inches)
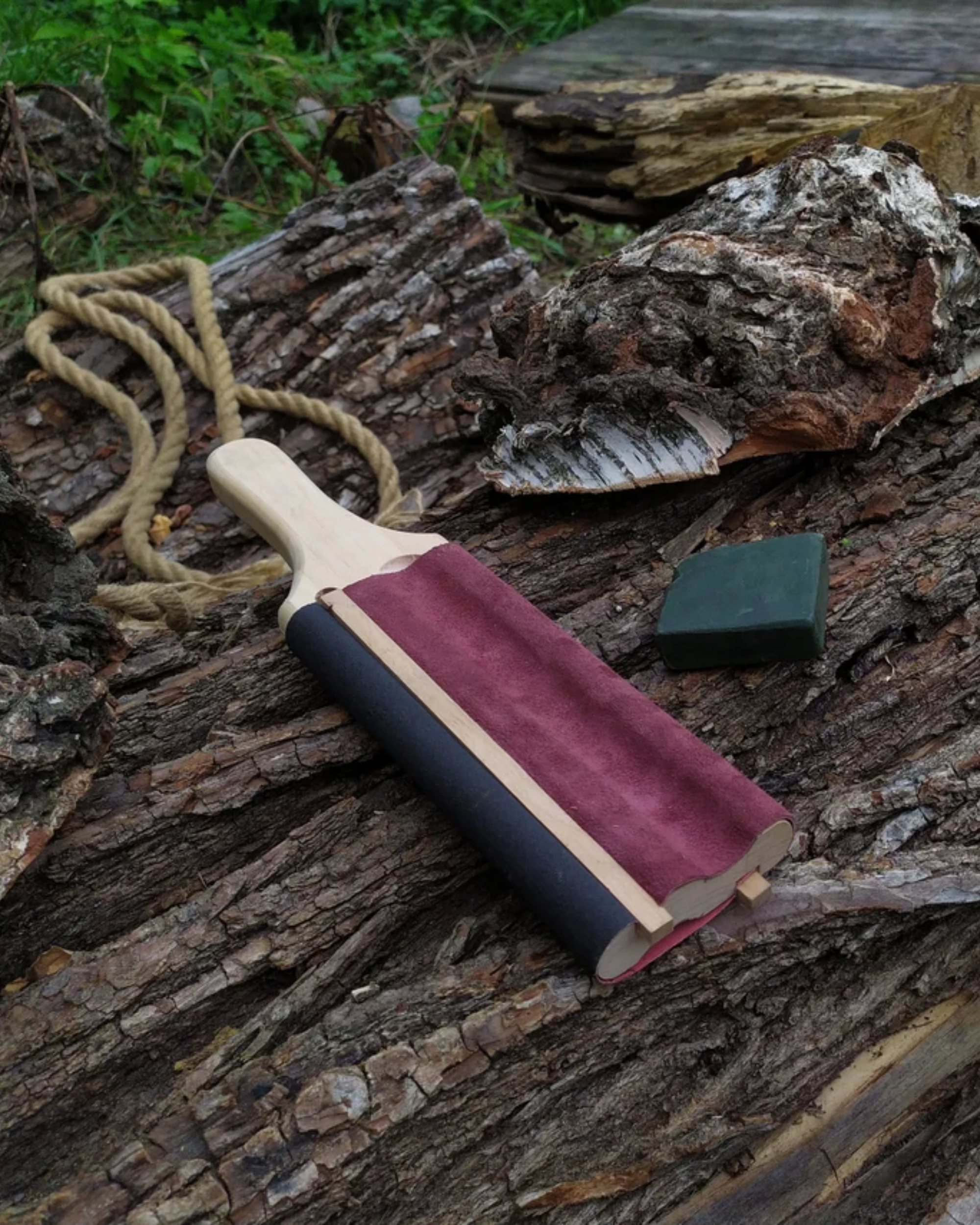
Hand-Forged Sloyd Knife, 7.5 cm (2.95 inches)
7-Piece Long Timber Framing Chisel Set
Chip Carving Knife, blade 3 cm (1.2 inches)
Overview of Wood Carving
Wood carving is the art of transforming wood into decorative or functional items. If you have ever dreamt of honing your whittling or sculpting skills, give it a try.
Such projects suit both beginners and professionals, and help understand wood properties better, as different woods react differently to carving. Anything from a small wooden spoon to a larger detailed furniture piece can be created using wood carving techniques.
It typically requires a few standard wood sculpting tools like knives, chisels, mallets, and gouges. A professional set is often more versatile, including hook knives, specialized gouges, V-tools, and power carving tools like dremels for hardwoods.
However, it is a common misconception that beginner wood carvers need a very expensive, high-end toolset. This belief creates a lot of barriers to entry. Experienced craftsmen recommend starting with a basic set of wood shaping tools and expanding the collection as experience grows.
Choosing the right wood carving tools directly impacts the quality of work and safety. We will examine this issue in more detail below and provide some tips on how to choose the best tools for carving.
Understanding Different Types of Wood Carving Tools
Let’s look at the different uses for the most essential wood carving tools and their specs to better understand when you may need each particular tool and which of them are multipurpose.
Knives, Chisels, and Gouges
Knives
Knives are front and center when it comes to wood carving tools. Some of their common characteristics include:
Blade grind
Type: Most wood carving knives feature a completely flat or Scandi grind. This type of grind provides precise cutting and a sharp edge, which can be easily cleaned.
Angle: The average grind angle is between 20-25 degrees, making it perfectly sharp and durable.
Blade
Tip: The tip is often pointed for making precise and controlled carvings. Rounded tips are used for smoothing and shaping surfaces, allowing for even distribution of pressure and preventing the risk of digging deep into the wood.
Length: Length may vary depending on the intended use. Shorter blades increase control over detailed patterns, while longer blades provide more comfort when roughing out a piece of wood.
Material
Blade: High-carbon steel is preferred for keeping edge sharp and the ease of sharpening. This type of steel has a higher hardness rating (58-62 HRC), making these wood carving tools more durable and resistant to wear. Stainless steel provides more rust and chipping resistance but may be tougher to sharpen. Its hardness rating is typically around 54-58 HRC.
Handle:
Typically made of hardwoods or synthetic materials. Professionals advise trying different handles to find one that fits your hand well. Knives with a full tang construction offer more durability and are usually considered safer. Look for ergonomic handles that allow for comfortable grip.
Recommended techniques:
Push cuts: Apply pressure with your thumb to push the blade for more controlled cutting actions. This technique is ideal for carving fine details and smaller carvings.
Pull cuts: Draw the knife towards yourself to make deeper, more forceful cuts, removing larger chunks of wood.
Sweeping cuts: Move the blade in a broader motion across the wood. This technique is particularly effective when working on rounded or curved shapes, like inside a bowl or a spoon.
Detail cuts: Use light, steady strokes with minimal pressure to create intricate designs.
Some of the common types of carving knives:
- General carving knives: Multipurpose tools for carving. Suitable for roughing out shapes, making broad cuts, and medium to large projects like basic sculptures or wooden spoons.
- Detail carving knives: Great for adding small, precise, delicate details to carvings. They are not multipurpose, as they are designed for ornamental work, not roughing out wood.
- Chip carving knives: Ideal for creating geometric patterns, chips, and fine cuts on flat surfaces. Their use is limited to chip carving.
- Hook knives: Created for making concave shapes and hollowing out bowls and spoons, forming curved, smooth lines.
Chisels
Chisels are essential for shaping and cutting wood, available in various shapes and sizes. Their common characteristics include:
Blade grind
Type: Usually have a flat grind with a sharp, durable edge.
Angle: The bevel angle ranges from 20 to 30 degrees. Lower bevel angles are ideal for fine details, while higher bevel angles are designed for heavy use like chopping or rough shaping. Higher angles are more durable, but more difficult to push through the wood.
Blade type and tip
Shape: Some of the most widespread types include straight, skewed, and fishtail chisels. They all serve different purposes.
Tip: Tips can be flat, rounded or v-shaped to make different cuts and fine details.
Length: Typically varies between 1 to 6 inches. Longer blades are suited for roughing out wood, while shorter blades are used for detailed projects.
Material
Blade: Typically made either of high-carbon steel or stainless steel, with the first one being more high-carbon being more durable and easy to sharpen and stainless steel being more weather resistant.
Handle: Usually are made of wood like ash or beech or synthetic materials.
Recommended techniques:
Push cuts: Use the body weight to push the chisel through the wood for controlled cuts.
Paring cuts: Create fine details by slicing thin layers of the wood.
Chopping cuts: Suitable for rough shaping. Push the chisel with a mallet to remove larger pieces of wood.
Common types of wood carving chisels:
- Straight chisel: Used for general purposes like creating straight surfaces and cuts.
- Skew chisel: Suitable for cleaning tight corners and typically used for angled cuts.
- Fishtail chisel: Suited for making delicate cuts, especially in tight spaces.
- Gouge: A type of the wood crafting tools used for making concave shapes and hollowing.
Gouges
At this point you might wonder how chisels differ from gouges. The primary differences between these carving tools for wood are in blade shape and grind. Unlike chisels with a straight cutting edge, gouges feature curved cutting edges that help create curved lines in carvings. This curved grind is also called ‘sweep’. The sweep varies depending on the degree of its curvature. The blade tip of gouges is often rounded or v-shaped.
Materials for handles and blades would be the same as for chisels, but the techniques used for gouges differ:
Sweeping cuts: Wide, sweeping motions to carve wood. Ideal for creating hollow or curved shapes.
Stop cuts: A series of small cuts to better control the depth and direction of your carving.
Paring cuts: Used in detailed projects to shave off the wood with a slicing movement.
Mallets and Hammers for Wood Carving
Mallets and hammers are good companions of chisels and gouges. Hammers are often used for heavy-duty tasks like removing larger chunks of wood and are better suited for working on harder woods. Mallets help apply force to chisels, providing more control over the carving and avoiding damage to the chisel.
These two categories of carving tools for wood help control the impact of cuts.
Mallets and their main characteristics
Shape: Usually have rectangular or cylindrical heads.
Material: Heads are often made from hardwoods. Some modern mallets feature synthetic heads (urethane heads) to better absorb vibration.
Weight: Ranges from 12 to 24 oz (340-680 g), depending on the mallet intended use.
Advantages:
- Help maintain better control over the force applied to chisels or gouges.
- Help reduce hand and arm fatigue and increase motion efficiency.
- Help make delicate cuts more precise.
Examples:
- Carver’s mallet: Suited for detailed carving project.
- Joiner’s mallet: Great for heavier tasks like chopping mortises.
Techniques:
- Controlled taps: Light taps help with carving fine details, while heavier strikes assist with roughing out wood.
- Angles control: Experiment with different angles for mallet strikes to achieve better quality of cuts.
Hammers and their main characteristics
Shape: Flat or slightly rounded heads.
Material: Hammer heads are often made from steel, with handles materials varying from wood to metal.
Weight: Hammers are typically heavier than mallets. Their weight ranges from 16 to 32 oz (453-907 g).
Advantages:
- More suitable for heavy use and hardwoods, as they provide more forceful movements.
- Can be used in a variety of tasks beyond wood carving.
Examples:
- Dead blow hammer: Filled with sand or lead shot to reduce vibration and provide more controlled strikes.
- Rubber mallet: Used for assembling without damaging the wood piece.
Techniques:
- Firm strikes: Applied to make firm, controlled strikes.
Sharpening Tools for Carving Blades
Tools for wood carving like knives, chisels, gouges have versatile blade shapes and angles that require specialized sharpening techniques to ensure they remain lazer-sharp and allow you to achieve smoothness in the final work. Let’s now take a closer look at their types and uses.
Sharpening stones
Materials: Made of aluminum oxide, silicon carbide, or natural stones.
How to use them: Keep the angle the same when moving the blade back and forth or in a circular direction.
What tools to sharpen: Knives, chisels, gouges, and other wood sculpting tools.
Leather strops
Materials: Leather with a smooth surface, used with aluminum oxide compounds or without them.
How to use them: Use a leather strop after sharpening with stones. Move the blade backward along the strop to refine the edge.
What tools to sharpen: Knives, chisels, and gouges.
Diamond plates
Materials: Steel plates covered with industrial diamonds.
How to use them: Efficient for quick sharpening of chisels wood and bent gouges. You may need to apply water or oil to the diamond plate before use. Move the blade across the diamond blade at a consistent angle.
What tools to sharpen: Knives, chisels, and gouges.
Sandpaper
Materials: Aluminum oxide (most common abrasive material, ideal for sanding wood, metal, painted surfaces).
How to use them: Used for edge sharpening. Move the blade in a circular motion or back and forth. Start with a coarse grit to remove the damaged edge parts of the blade and then move to finer grits.
What tools to sharpen: Knives and chisels.
Some additional tips
Collet size. If you use a die grinder for sharpening woodworking carving tools, ensure the correct collet size. The recommended collet size is either ¼ inch or ⅛ inch. ¼ is versatile and can be used for sharpening, grinding, and polishing. ⅛ inch collet allows for more detailed work.
Storage. Keep your tools set organized in a canvas case to protect them from damage.
Tips for Choosing the Right Wood Carving Tools
When choosing wood crafting tools, consider the projects you would like to start and the carving technique they may involve.
As your practice and experience grow, you may want to take on more sophisticated and larger projects. At this point, consider investing in specialized wood crafting tools.
But how do you identify the quality of tools for wood carving? You might visit forums or online groups where carvers discuss the lessons they learned when they first started and the types of tools they used.
Based on the information we provided earlier, some of the key features that quality wood carving tools should have include:
- Steel: Look for high-carbon steel with hardness rating 58-62 HRC for better edge retention.
- Handle: Ergonomically designed hardwood or synthetic handles to prevent fatigues during long carving sessions.
- Weight: The tool’s weight should be perfect for delicate and heavy duty tasks, so first define the project you want to perform, and then select the basic tools you will need.
- Versatility: The best wood carving tools set includes knives, chisels, and gouges. Hammers and mallets can be supplementary if they simplify your carving process.
- Sharpness: Tools should come well-sharpened out of the box, and the sharpening process overall should be straightforward.
Conclusion: Investing in Your Wood Carving Journey
To sum up, starting with a basic tools set, including knives, chisels, gouges, and mallets/hammers, is sufficient to perform versatile carving projects and develop your skill in different carving techniques.
As you gain experience, you may choose to expand your collection of woodworking carving tools. You might also find that some tools become redundant, as you focus more on specific types of carving, like whittling or chip carving.
It’s crucial to note that you don’t need very expensive tools to achieve high accuracy in your designs. At the end of the day, it’s not the tools that define the carver, but your carving style and practice.